Green facilities design in the oil and gas industry is a forward-thinking approach that prioritizes sustainability, environmental responsibility, and energy efficiency throughout the entire lifecycle of facilities. It aims to minimize environmental impact at every stage, including resource extraction, production, and utilization. Green facilities design represents a shift toward environmentally conscious practices, aiming to balance industry needs with responsible resource management and emissions reduction.
In this article, the author will highlight the Top 4 “green facilities” design applications that are becoming a trend in the latest development. In the present time, most of the projects which are funded by the International Finance Corporation (IFC) have a “green facilities” design as their mandatory requirement. The author lines up the "green design" subject implementation below based on their cost application magnitude for easy understanding,
Closed Loop Flaring – Flare Gas Recovery System
Flare Gas Recovery (FGR) represents a set of specialized compression packages designed to tackle gas flaring. Gas flaring is the practice of burning excess or waste gases produced during industrial processes, especially in the oil and gas sectors and chemical production. These industries often generate associated gases, which, if left uncontrolled, significantly contribute to harmful emissions released into the atmosphere. Flaring these gases has been a common and wasteful practice, raising environmental sustainability concerns.
FGRS is designed to recover and repurpose gases and emissions that would traditionally be burned during the flaring process. Key components include methane, liquefied petroleum gases (LPGs), and sulfur dioxide, all of which have a detrimental impact on the environment when released into the atmosphere. The recovery process involves capturing the gas from the flare knock-out vessel and compressing it using specialized equipment (often liquid ring compressors).
Compression ensures safe handling of these gases and makes them available for reuse. The recovered gases can be reintegrated into the facility’s fuel gas system, reducing the need for external energy sources or tank blanketing (in FPSO). It can be used also as valuable refinery feedstock, contributing to a more circular and sustainable economic model.
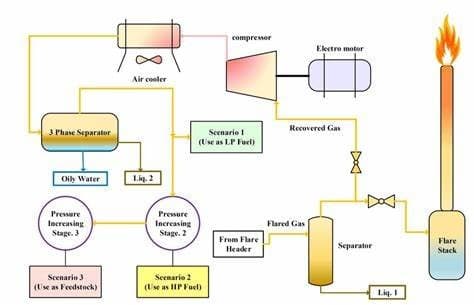
Figure 1 Typical Flare Gas Recovery System Schematic
Advance Produce Water Treatment
Produce water discharge is becoming one of the crucial criteria at the present time. In the old time, 30-40 ppm oil content criteria are quite standard. Today, several Oil and Gas Companies have targeted the oil discharge criteria below 10 ppm. This requirement is no longer possible to be tackled by the conventional primary (such as CPI, API basin) or Secondary (such as: Compact Floatation Unit, Hydro cyclones) produced water treatment. It will use complex tertiary produce water treatment technology such as ultra-filtration, Biological treatment, or Reverse Osmosis to reach the discharge criteria. One of the drawbacks of this design is the high carbon footprint requirement for the facilities on top of the increase in produce water system cost.
Rotating Equipment Electrification
To reduce carbon emissions, rotating equipment electrification had a significant contribution. Big compressors which previously came with the “Gas Turbines Driven” are replaced by the Electric driver which today have more reliability compared to their performance decades ago. This concept of course will increase the overall facility's power demand since the big compressor engine normally consumes between 20-30 MW capacity above 100 MMSCFD. Internal gear compressor is now introduced on the upstream application instead of the conventional centrifugal to reduce the power consumption between 15%-25%.
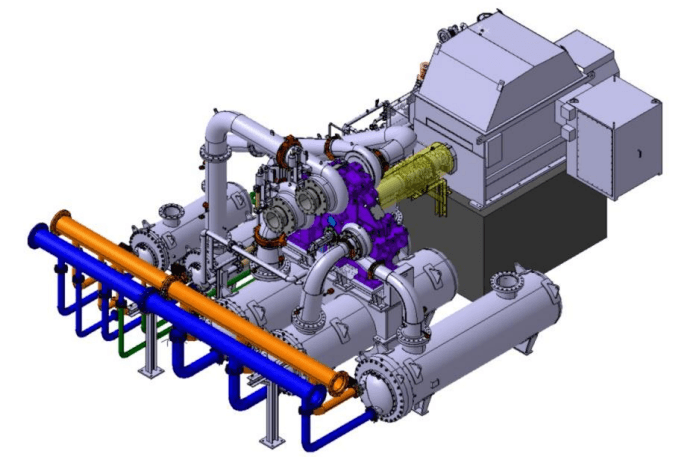
Figure 2. 3D model view of Integral Compressor
Combines Cycle Power Generation
The application of the three points above systematically increases the power demand as an energy penalty. This is where the combined cycle of Power Generation plays its role in optimizing the power generation. A combined cycle power plant is an assembly of heat engines that work in tandem from the same source of heat, converting it into mechanical energy. The first component is a gas turbine, which operates using the Brayton cycle. It burns natural gas or oil to produce high-temperature, high-pressure exhaust gases. The second component is a steam turbine, which operates using the Rankine cycle. It utilizes the heat from the gas turbine’s exhaust to generate additional power.
The gas turbine produces mechanical energy by expanding the hot exhaust gases. However, these gases still contain significant heat energy. Steam turbine captures this remaining heat by passing the exhaust gases through a heat exchanger. In the heat exchanger, the exhaust gases transfer their heat to water or steam, which drives the steam turbine. The combined cycle power plant thus combines the output of both turbines to generate electricity more efficiently than a standalone gas turbine or steam turbine.
Petrobras had ongoing 2 FPSO P-84 project and P-85 with all-electric concept plus combined cycle power generation. MODEC also had BM-C-33 with Equinor ongoing for combined cycle implementation. Both projects are expected to present a 20-30% carbon footprint reduction
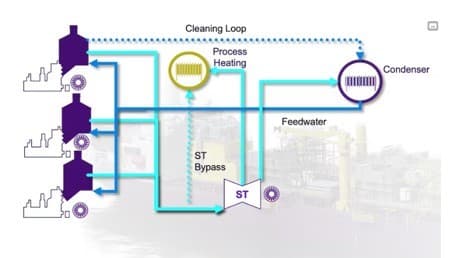
Figure 3. Typical Combined Cycle Schematic
As we close this article, let us remember that green design isn’t just a luxury or nice to have at the present time; it’s a necessity and our obligation to contribute to a sustainable environment. Our facilities no longer stand as solitary sentinels; they dance with the wind, hum with the tides, and cradle life beneath their steel feet. So, let the waves carry our commitment, and may the sun rise on a greener horizon 😊.